
Rhinoceroses are some of the largest remaining megafauna: all weigh at least one tonne in adulthood.
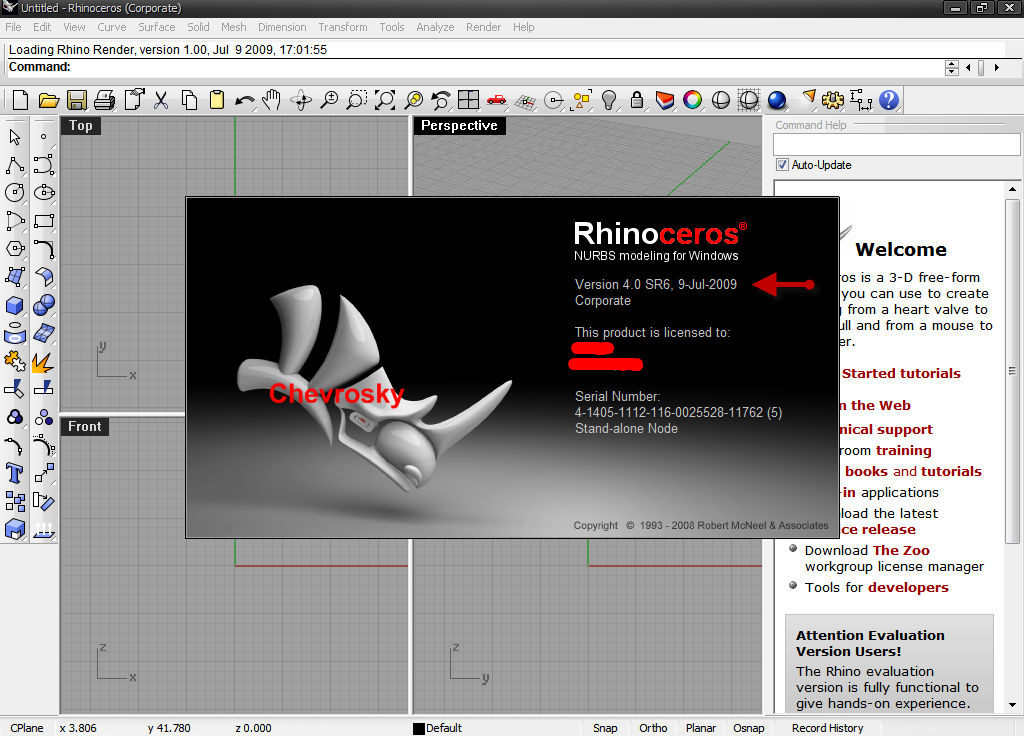
Two of the extant species are native to Africa, and three to South and Southeast Asia. Rendering time can vary depending on assembly size, reflectivity, transparency of parts, and a few other variables.A rhinoceros ( / r aɪ ˈ n ɒ s ər ə s/ from Ancient Greek ῥῑνόκερως ( rhīnókerōs) 'nose-horned' from ῥῑνός ( rhīnós) 'nose', and κέρας ( kéras) 'horn' ), commonly abbreviated to rhino, is a member of any of the five extant species (or numerous extinct species) of odd-toed ungulates in the family Rhinocerotidae (it can also refer to a member of any of the extinct species of the superfamily Rhinocerotoidea). For example, you can set your solid bodies to be “made of” marble, wood, various metals, glass, and more before changing the Environment Style with a choice of 8 different styles and be able to rotate the light source to control where highlights show up on your design.įusion 360 gives you the right to choose the type of rendering process, it can be quick, normal, or advanced. You need first to apply materials to your design with the workflow, and you can give specific material attributes to your model. You will also notice the toolbar has tools to control materials, environment, and quality of rendering. in the rendering workspace, you will see the background and model change a little as it is being optimized for visualization.
#Rhinoceros software 5 version 4 differences Patch
In Fusion 360, you just have to head over to the model or patch icon and hover over it to get a flyout that lets you select render. Animations and Simulations Fusion 360 VS Rhino?īoth Fusion 360 and Rhino offer their users a rendering option to create renders that can give a realistic view of the product and a clearer vision of a conceptual design than a plotted drawing. Adapted to additive manufacturing, the advantages of Rhino are not limited to this sector. You can indeed develop technical drawings and illustrations, thus communicating your ideas more easily. Your 2D creations can also benefit from the strengths of Rhino, thanks to the features of Make2D. You will find all the basic tools, transformation tools, points, curves, or surfaces. Rhino provides access to a wide range of tools to develop your projects, whatever your field. This modeling technique is the most precise out there. This type of modeling allows us to optimize the number of facets making up the surface of the object. You can, therefore, create your surface in three dimensions by making changes on curves. This technique involves performing modeling by working on curves rather than connecting polygons and vertices. Rhino, on the other hand, uses the curve modeling technique, with non-uniform rational B-splines (NURBS or Non-Uniform Rational Basis Spline).
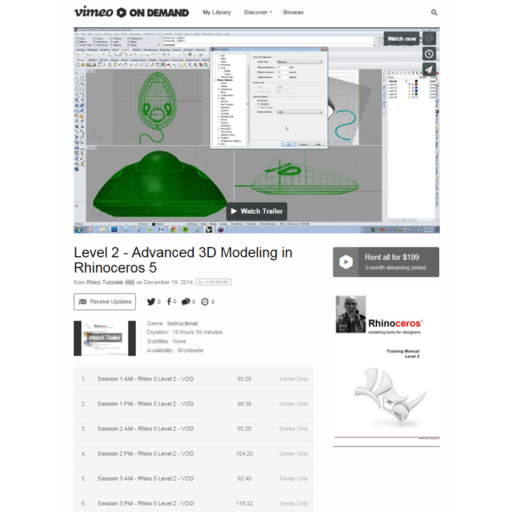
Long story short, Fusion 360 comes with many tools that should always be combined to make the process of designing products easier and give better results.

The third is polygonal modeling, which allows: the creation of organic or ergonomic shapes in the software’s sculpt space, creation of a Tspline from primitives (boxes, cylinder, etc.), creation from profiles (closed curves) by extrusion, sweeping, and the possibility of transforming a surface created from the Model environment or Patch into a T-spline to edit the shape. In this environment, a closed solid can be decomposed into its constituent surfaces. It contains surface creation tools (extrusion, sweep, etc.) that allow surface creation based on sketch profiles. The relationships between sketch elements and dimensions are defined in the sketch and reflect the design intent. The first is parametric modeling, which is based on 2d sketches forming a closed network of curves (Profile). Fusion 360 can be used for different types of modeling, from technical details to organic surfaces.
